
WORK-PIECE BALANCING ANALYZER ( WBA )
High efficiency, High precision, Suitable for short / thin work-piecesIncreasing productive efficiency and streamlining operations have always been Goodway's research and development concept. The Goodway Work-piece Balancing Analyzer ( WBA ) is based on the developing foundation of our multi-tasking turning centers and University - Industry Cooperation. And now we combine them together to accomplish for a higher level of efficiency and streamlining.
The WBA is mainly applied to "Dissymmertical parts" and "workpiecs that needed to be balanced after machining" . The sensor installed inside the machine can pick up the vibration signal caused by the centrifugal force under high speed rotation from the work-piece. For dissymmertical parts, the machine is able detect the unbalanced position and weight and provide information for the user to design the appropriate tooling. For work-pieces that needed to be balanced after machining, by using our multi-tasking turning centers ( more than 3 axes machines ), the unbalanced position and weight can be detected online and be eliminated by the live tooling turret during the machining.
Before / After correction comparison chart
Before WBA correction

After WBA correction
Vibration
⇓ 88%
ApplicationsTake disk brake as an example, most companies use offline balancing analyzer method, which the machine needs to be stopped after the disk is finished, then move to the balancing analyzer for detection. When the detection is done, then move the disk to a machining center to eliminate the unbalance amount. It costs unwanted time by just loading and unloading the disk from one place to another, it can also cause accuracy error.
Therefore, we created the concept of installing the WBA into the vertical multi-tasking turning center. When the disk brake is finished, it can be evaluated online, then use C-axis to eliminate the unbalanced amount. This can save lots of loading and unloading time and also prevent accuracy error from the process. With the combination of the WBA and multi-tasking turning procedure, we can bring multi-tasking advantages into the next level.
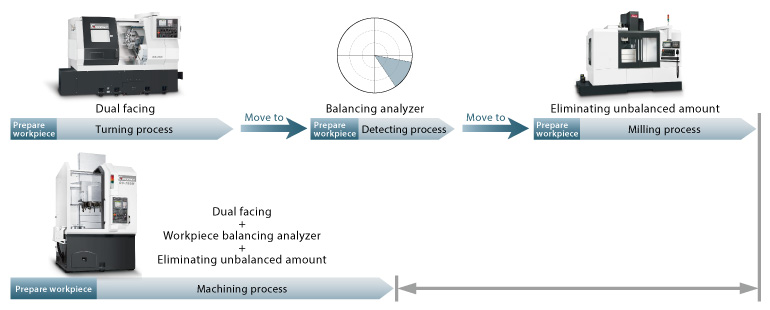
Cycle time ⇓ 50%
The interface of the WBA can be customized based on customer's needs, which is easy to use. Take disk as an example, the standard work-piece only takes 2 minutes to setup. First insert the disk data, then insert machining parameters. After the setup is done, it only needs one button to begin the entire procedure ( turning, detecting, milling ) which the cycle time is only 3 ~ 4 minutes.
Work-piece balancing analyzing specificationsCapacity | WBA |
---|---|
Disk diameter | 286 ~ 355 mm |
Disk thickness | 28 ~ 32 mm |
Disk friction surface | 60 mm |
Correction method | Single side correction |
Unbalance amount | 1,650 ~ 14,850 g-mm |
Sensitivity | 0.001g |
Balancing grades | ISO 1940, G2.5 |
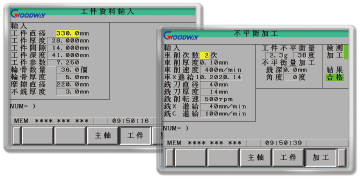
Insert disk data
Insert machining parameters
